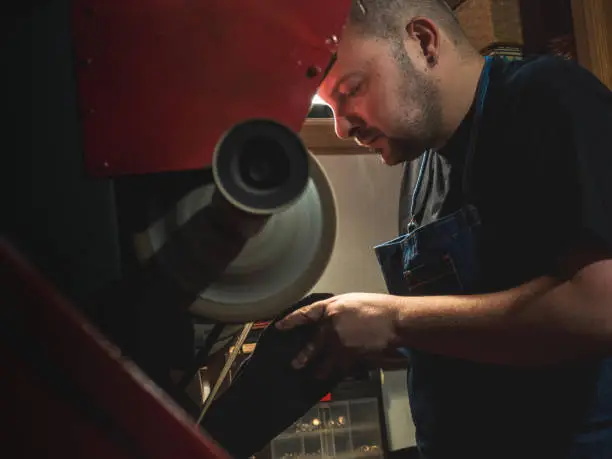
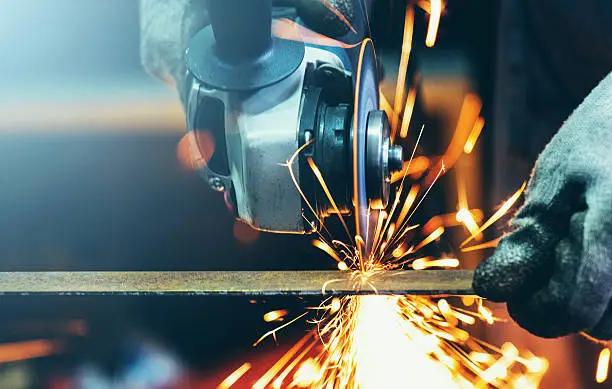
Choosing the Right Metal for Spinning: A Comprehensive Guide
Metal spinning is a versatile and highly specialised manufacturing process that transforms flat metal discs into complex, symmetrical shapes without the need for welding or joining. However, the success of any metal spinning project heavily relies on selecting the correct type of metal. This decision is crucial, as the material’s properties, durability, and application requirements directly influence the final product’s quality and performance.
This blog will guide you through the essential factors to consider when choosing the best metal for your spinning project, providing insights into material properties, durability, and typical applications.
Factors to Consider When Choosing a Metal for Spinning
Selecting the right metal for spinning is not just about compatibility with the process; it’s also about ensuring the finished product meets its intended purpose. Different metals respond uniquely to the high-pressure, high-speed spinning process. Factors such as malleability, strength, and resistance to wear must align with both the manufacturing requirements and the application needs of the product.
Key considerations include:
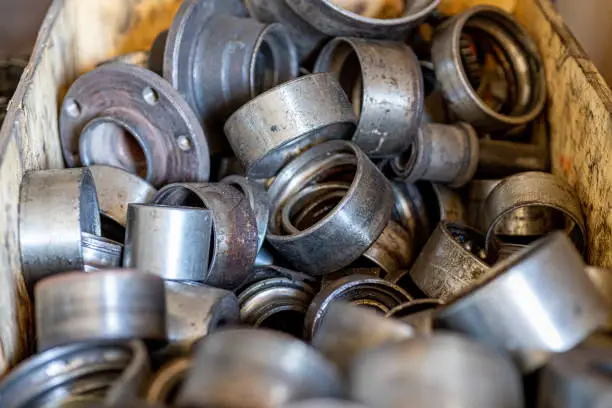
- Material Properties
The malleability and ductility of the metal will determine how easily it can be spun. For example, metals with high ductility, such as aluminium and copper, are better suited for intricate designs and complex geometries.
- Durability Requirements
If the product will be exposed to extreme conditions, such as high temperatures or corrosive environments, materials like stainless steel or brass are better suited due to their resistance to wear and corrosion.
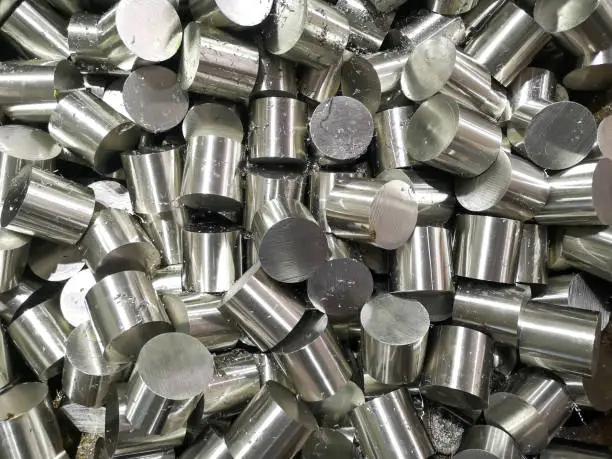
- Application Needs
Understanding the end-use of the product is vital. For instance, food-grade applications demand materials like stainless steel, which are non-toxic and resistant to bacterial growth. Alternatively, electrical components benefit from the superior conductivity of copper.
- Aesthetic Appeal
For decorative items, the appearance of the metal plays a significant role. Brass and copper are often chosen for their distinct finishes, while aluminium provides a modern, sleek look.
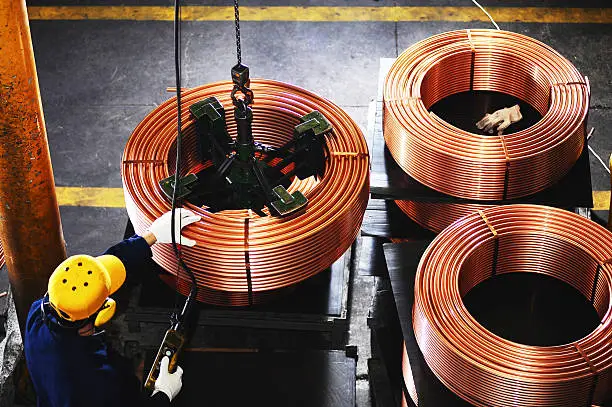
- Cost Considerations
Budget constraints often influence material selection. Aluminium and carbon steel are cost-effective options, while stainless steel and brass may be pricier but offer greater durability and aesthetic appeal. Titanium, while expensive, provides unmatched performance for specialised applications.
- Environmental Impact
In today’s manufacturing landscape, sustainability is an important consideration. Recyclable materials such as aluminium and stainless steel are excellent choices for reducing environmental impact and aligning with eco-friendly goals.
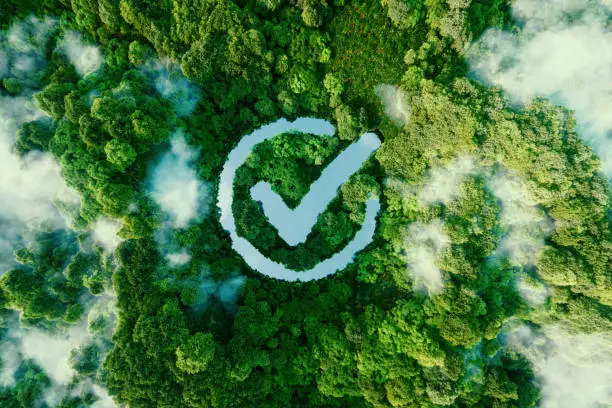
Common Metals Used in Spinning
Here are the most commonly used metals in spinning, along with their properties and typical applications:
- Aluminium
Aluminium is a lightweight, corrosion-resistant metal widely used in spinning projects. Its malleability makes it easy to work with, and it is ideal for applications requiring lightweight yet durable materials.
Aluminium is a lightweight material with high corrosion resistance and excellent thermal conductivity. Typical usage is in aerospace components, kitchenware such as pots and pans, and lighting reflectors.
- Stainless Steel
Stainless steel is renowned for its strength and resistance to corrosion, making it a popular choice for products that must endure harsh environments or rigorous use.
Stainless steel offers high tensile strength, excellent resistance to rust and corrosion, and an aesthetic appeal due to its shiny finish. Typical applications include food processing equipment, medical instruments, and decorative architectural elements.
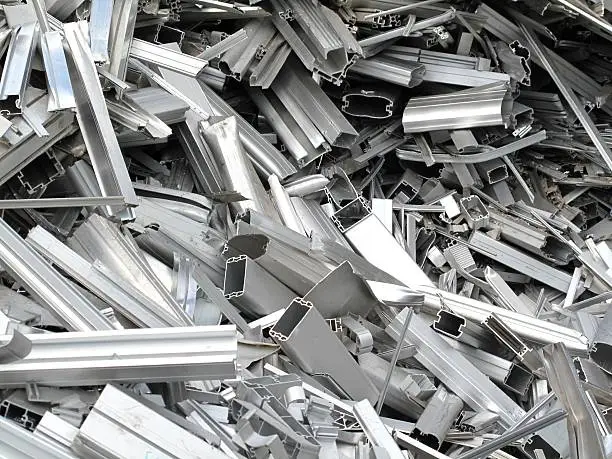
- Copper
Copper is highly malleable and has excellent electrical and thermal conductivity, making it ideal for both functional and decorative applications.
Copper also has a natural resistance to bacteria and an attractive reddish finish. It is often used in electrical components, plumbing fixtures, and decorative items like bowls and sculptures.
- Brass
A copper-zinc alloy, brass offers an appealing balance of malleability and durability. Brass has excellent corrosion resistance and a distinctive golden appearance, making it popular for decorative use. Applications include musical instruments, light fixtures, and ornamental hardware.
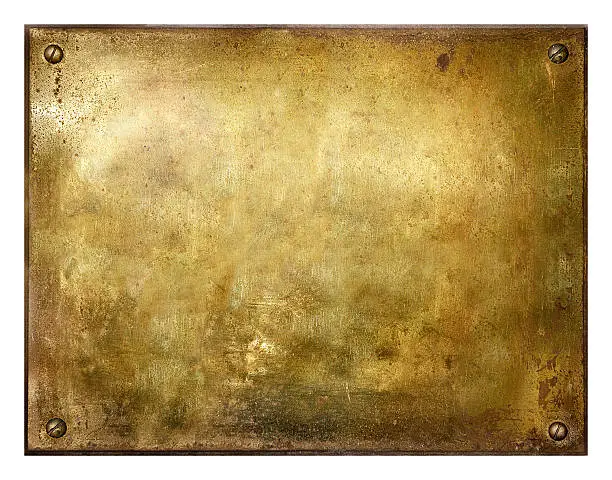
- Carbon Steel
Carbon steel is an affordable and robust material, often chosen for industrial applications requiring strength and durability.
Carbon steel is known for its high tensile strength, excellent wear resistance, and cost-effectiveness. Common uses include automotive parts, industrial machinery, and structural components.
- Titanium
Titanium combines lightweight properties with exceptional strength and corrosion resistance, making it a premium choice for high-performance applications.
Titanium features a high strength-to-weight ratio, exceptional corrosion resistance, and biocompatibility. It is often utilised in aerospace components, medical implants, and high-end sporting goods.
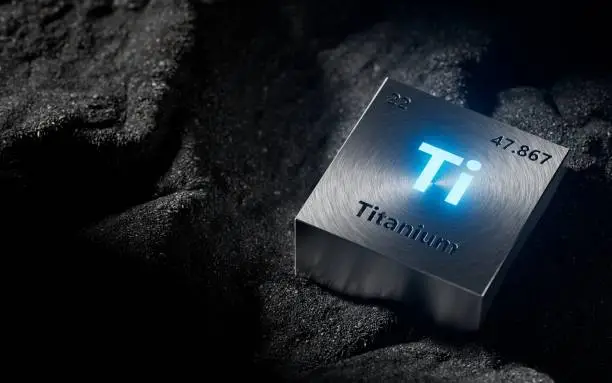
Enhancing Your Metal Spinning Project
At Tanfield Metal Spinners, we understand the importance of choosing the right material for your spinning needs. With the most extensive tooling range in the UK and decades of expertise, we can help you navigate the complexities of material selection to ensure your project’s success. Our flexible and responsive approach allows us to deliver high-quality, customised solutions tailored to your specific requirements.
Whether you’re developing aerospace components, architectural elements, or decorative pieces, our team of experts is here to guide you every step of the way. We work closely with you to identify the ideal material, considering your project’s unique demands and budget considerations.
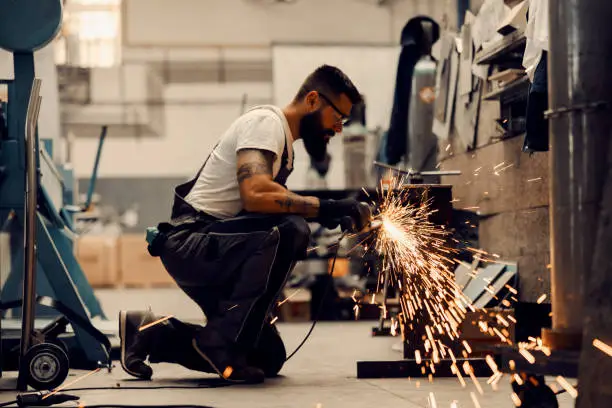
The Future of Material Selection in Metal Spinning
As technology advances, so does the range of materials available for metal spinning. Emerging alloys and composite materials are opening new possibilities, enabling manufacturers to achieve unprecedented levels of performance and efficiency. For example, developments in titanium alloys and advanced stainless steels offer enhanced properties that cater to the demanding requirements of industries like aerospace and healthcare.
At Tanfield Metal Spinners, we remain at the forefront of these innovations, continually adapting our processes and capabilities to provide cutting-edge solutions for our clients.
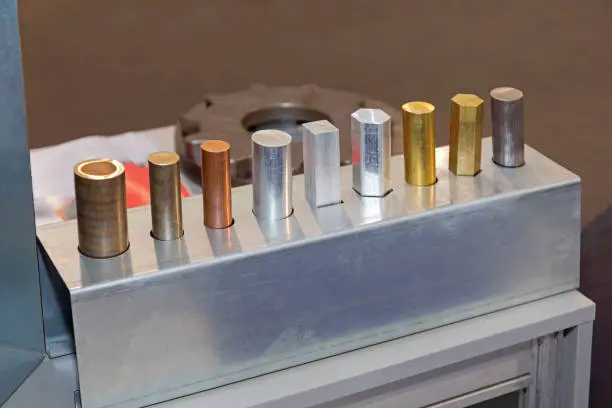
Making the Right Metal Spinning Choice
Choosing the right metal for spinning is a critical decision that impacts the functionality, durability, and overall success of your project. By understanding material properties, application needs, and cost considerations, you can make an informed choice that aligns with your goals.
Partner with Tanfield Metal Spinners to bring your vision to life with precision and excellence. With our expertise and commitment to quality, we ensure your metal spinning project achieves the highest standards. Contact us today to discuss your next project and discover how we can help you achieve outstanding results.
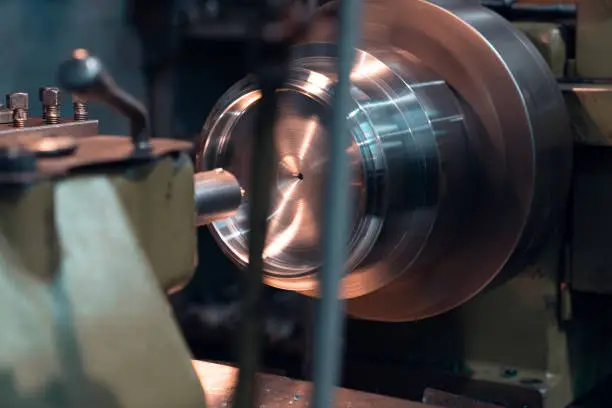